Preparing Hatseflats for outings
Preparing Hatseflats for a long trip is very different from a daysail.
I prefer to not take too much on board, so for every outing I must decide what I will actually need.
It might be easier to always have everything on board but it saves a lot of weight if you leave ashore
what you don't need (and the stuff that you don't need will last longer in your garage than in your damp boat).
Preparing your boat like this for every outing requires extra work and is only feasible with good work lists and checklists.
Work Lists
I have put some work lists to perform for trips with Hatseflats.
Maybe they are useful for others too.
Preparing the 'Hubert' container
This is a small watertight container for emergencies.
It has my name and phone number on it.
- Opinel 8 knife
- Hand gel for clean hands (no water required)
- headlamp
- cigarette lighter
- mosquito spray and net
- pen
- medicine for 2 days - more in toiletry bag.
- room for 2 smart phones and watertight bags
- sunscreen SPF30 or SPF50
- toothbrush
Preparing the 'Hatseflats' container
This is a small watertight container with small items specific to Hatseflats.
- sailors knife
- handheld VHF
- handheld GPS
- anemometer
- handheld compass
- binoculars
- medicine for 2 days (again!)
- wrench #13 for M8 nuts
- sunglasses for skipper
- 2 lightweight isolation blankets
- 2 lightweight rain ponchos
- grease for oar leathers
- 1-2 plasters (more in First Aid box)
Preparing the electronic devices
- charge VHF
- charge batteries for GPS
- charge PowerBrick
- charge GoalZero powerbank with 4AA batteries
- charge GoPro
- charge batteries for nav lights
On longer trips it is handy to bring:
- nav lights
- 230V/12V charger for VHF
- solar panel to charge the powerbanks
Preparing the Galley Box
- cutlery: Opinel 8 knife, 2 sporks, lighter, matches, pen, wooden spoon for cooking
- waste bags
- Campingaz burner with spare C306 cartridges
- Small cooking set with cooking pan, sauce pan, 2 folding cups, 2 beakers and 2 folding naps
- 2 plastic drinking glasses
- cutting board
- pepper and salt
- washing up liquid and sponge
- cooking oil (sunflower or olive)
- 1-2 drying cloths
- instant coffee, tea bags
On longer trips it is nice to bring the Bialetti percolator and ground espresso coffee.
Preparing Documents
- car insurance policy including cover for passengers, green card
- boat insurance policy
- trailer insurance policy
- Vaarbewijs
- VHF certicficate and registration
When sailing abroad we will need to bring passports and a travel insurance policy (to repatriate us if we die on holiday).
Preparing Car and Trailer
Car:
-
Check tyre pressure (2.4 bar)
Increase to 2.4 forward and 2.8 aft when heavily loaded.
-
Put certified trailer lock in boot.
-
Grease ball of towing hitch.
Preparing the trailer:
-
Check tyre pressure of road wheels (2.2 bar)
-
Check tyre pressure of guide wheels.
-
Ensure that the cushions are adjusted to support Hatseflats.
-
Add protective ring around mast to separate mast from transom.
-
Add webbing strap around aft part of Hatseflats.
-
Put transport cover on Hatseflats.
Checklists
The bare hull of Hatseflats weighs only 100kg but setting up for a quick sail already adds 82kg.
For a daysail you would take provisions, an anchor etc which takes the sailing weight up to 200kg.
The next big hurdle is to set the boat up for an overnight trip.
Adding the boat tent and camping gear adds another 35kg.
After that, camping for a week adds only 15kg.
Preparing for a longer trip is not helpful unless you are planning to spend weeks without access to shops.
On our recent trip on the Limfjord we found that Struer and Thisted had supermarkets but the smaller villages
did not have shops.
This means you must plan to visit a bigger town at least every week to stock up on your food.
Each of the checklists below builds on the previous one, so you must add the weights as well - a good brain training.
Preparing for a week-long camping trip means a total weight of around 250kg (without crew).
Checklist for Basic
Item |
Location |
Kg/1 |
Number |
Total Kg |
Comments |
Bare hull |
N/A |
100 |
1 |
100 |
|
Mooring lines fwd |
Foredeck |
0,25 |
2 |
0,5 |
|
Bailer |
Anchor Well |
0,1 |
1 |
0,1 |
|
Mast and halyard |
Anchor Well |
11 |
1 |
11 |
|
Sail with boom and yard |
Anchor Well |
13 |
1 |
13 |
|
Stout bucket |
Anchor Well |
1,4 |
2 |
2,8 |
|
Black fender and rope |
Anchor Well |
0,7 |
2 |
1,4 |
|
Daggerboard |
Bridge Deck |
4,5 |
1 |
4,5 |
|
Sailing trousers |
Bridge Deck |
1 |
2 |
2 |
|
Sailing Jacket |
Bridge Deck |
0,5 |
2 |
1 |
|
Racing Vest |
Bridge Deck |
0,4 |
2 |
0,8 |
|
Gloves |
Bridge Deck |
0,03 |
4 |
0,12 |
|
Crocs |
Bridge Deck |
0,24 |
2 |
0,48 |
|
Mainsheet 7mm |
Cockpit |
0,7 |
1 |
0,7 |
|
Seat |
Cockpit |
7 |
2 |
14 |
|
Floorboard |
Cockpit |
10 |
1 |
10 |
|
Paddle |
Cockpit |
0,7 |
1 |
0,7 |
|
Oar |
Cockpit |
3 |
2 |
6 |
|
Rudder Blade |
Transom |
4,5 |
1 |
4,5 |
|
Rudder Box |
Transom |
4 |
1 |
4 |
|
Orange fender and rope |
Cockpit |
0,7 |
2 |
1,4 |
|
Mooring lines aft |
Aft Deck |
0,25 |
2 |
0,5 |
|
Dry clothes |
Aft Deck |
2,5 |
1 |
2,5 |
|
First Aid Box |
Aft Deck |
0,5 |
1 |
0,5 |
|
|
|
|
|
|
|
Total |
|
|
|
182,5 |
|
Checklist for Daysail
Item |
Location |
Kg/1 |
Number |
Total Kg |
Comments |
Fisherman anchor |
Anchor Well |
10 |
1 |
10 |
|
Water bottles |
Bridge Deck |
0,5 |
4 |
2 |
|
Electrics |
Bridge Deck |
1 |
1 |
1 |
|
Hubert-container |
Anchor Well |
1,5 |
1 |
1,5 |
Curtec 7006 container to use as grab bag |
Hatseflats-container |
Anchor Well |
1,5 |
1 |
1,5 |
Curtec 7006 container with VHF, GPS, tools, knife etc. |
Emergency Flares |
Aft Deck |
1 |
1 |
1 |
|
Mooring pin |
Cockpit |
1 |
1 |
1 |
To be verified. |
Total |
|
|
|
18 |
|
Checklist for Overnighter
Item |
Location |
Kg/1 |
Number |
Total Kg |
Comments |
Boat Tent |
Aft Deck |
7 |
1 |
7 |
|
Crutch |
Cockpit |
2 |
1 |
2 |
Aft support for boat tent |
Mast Strut |
Cockpit |
1 |
1 |
1 |
Forward support for boat tent |
Nav light |
Aft Deck |
0,5 |
2 |
1 |
To be verified |
Sleeping Boards |
Cockpit |
2 |
2 |
4 |
|
Truss for sleeping platform |
Cockpit |
4 |
1 |
4 |
|
Clothes |
Foredeck |
0,5 |
2 |
1 |
Change of underwear, sweater |
Clothes bags |
Foredeck |
0,5 |
2 |
1 |
Waterproof compression bags with clear window |
Galley Box |
Cockpit |
10 |
1 |
10 |
|
Camping Light |
Foredeck |
0,3 |
1 |
0,3 |
|
Sleeping bags |
Aft Deck |
0,8 |
2 |
1,6 |
|
Mattress 200x50 |
Aft Deck |
0,5 |
2 |
1 |
|
Headcushion |
Aft Deck |
0,2 |
2 |
0,4 |
|
Sleeping gear bags |
Aft Deck |
0,5 |
2 |
1 |
Waterproof compression bags with clear window |
Bridge Deck hatch cover |
Bridge Deck |
1 |
1 |
1 |
|
|
|
|
|
|
|
Total |
|
|
|
35,3 |
|
Checklist for Week
Item |
Location |
Kg/1 |
Number |
Total Kg |
Comments |
Exrra Clothes |
Foredeck |
0,8 |
2 |
1,6 |
Extra underwear, shorts etc |
Extra Food |
Cockpit |
5 |
1 |
5 |
|
Food Container |
Cockpit |
2 |
1 |
2 |
Curtec 7026 container (26L) |
Helinox Chair Two |
Aft Deck |
1,5 |
2 |
3 |
|
Solar Panel |
Aft Deck |
0,5 |
1 |
0,5 |
|
Spare Tent |
Aft Deck |
3 |
1 |
3 |
|
Spare Daggerboard |
Cockpit |
4,5 |
0 |
0 |
Only for rocky venues. |
Total |
|
|
|
15,1 |
|
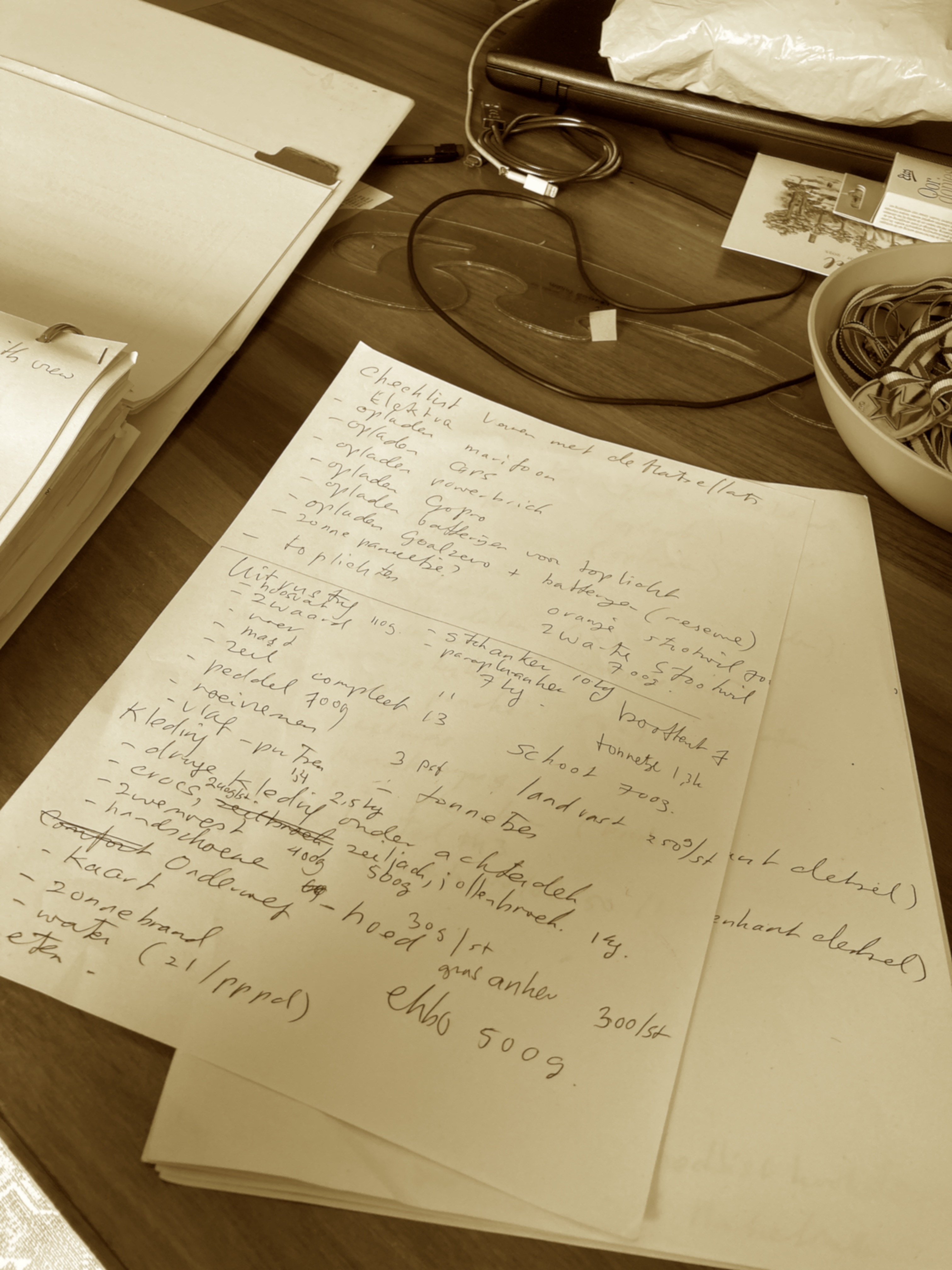
Checklists:always handy.
|