Foils Maintenance
While building Hatseflats I created a low tech daggerboard and rudder because I did not have much time.
The foils were made from 3x8mm plywood blanks and featured a rounded leading edge and straight tapered trailing edge to retain sufficient strength (compared to solid wood foils, plywood foils have only half the strength).
After five years of hard use the trailing edge and bottom edges of the daggerboard and rudder were severely bruised.
If I left Hatseflats in the water the foils would soak themselves full of water to make it very hard to pull the daggerboard out of its case.
The best solution would be to laminate blanks from planks and shape them properly for better upwind performance.
Laminated wooden foils are quite strong, especially if covered with 80g cloth and epoxy.
However, I did not want to discard the old foils
and decided to add a trailing edge and bottom edge made from of meranti.
I cut off the old trailing edge and bottom 2cm from the boards and glued meranti lengths in place.
Because the garage was too cold I did all the epoxy work in our attic.
First I glued the overlong trailing edges with clear epoxy into place.
In hindsight I should have saved much time by using liberal amounts of PolyPox 700 glue instead of clear epoxy.
As it was I had to recoat the trailing edge many times.
Once the trailing edges were cut to measure I glued and screwed the bottom edges to the boards with PolyPox 700.
After the epoxy had cured I bored out the screw holes and injected clear epoxy with a syringe.
This didn't go well because the excess epoxy just dripped out of the screw holes.
13 April 2024
Worked out a better solution for the screw holes to ensure that no water can soak into the plywood from the bottom edge.
Solution:
- Remove screws
- Drill the screw holes bigger so that a sufficient amount of epoxy can get in.
- Glue a little plastic ring around each screw hole (cut from plastic wall plugs)
- Once dry, drip clear epoxy into the screw hole right until the upper edge of each surrounding screw hole.
- Post-cure: file the plastic rings and excess epoxy away.
Result: all holes filled (and watertight) with epoxy right to the surface.
15 April 2024
Applied second and third coat of epoxy to trailing edges and bottom on one side.
18 April 2024
Applied second and third coat of epoxy to trailing edges and bottom on the other side.
What next?
Allow the epoxy to cure for at least 2 weeks before sanding and painting with two-pot PU paint (PolyService DD paint)
After that, wait at least 2 weeks for the DD paint to cure.
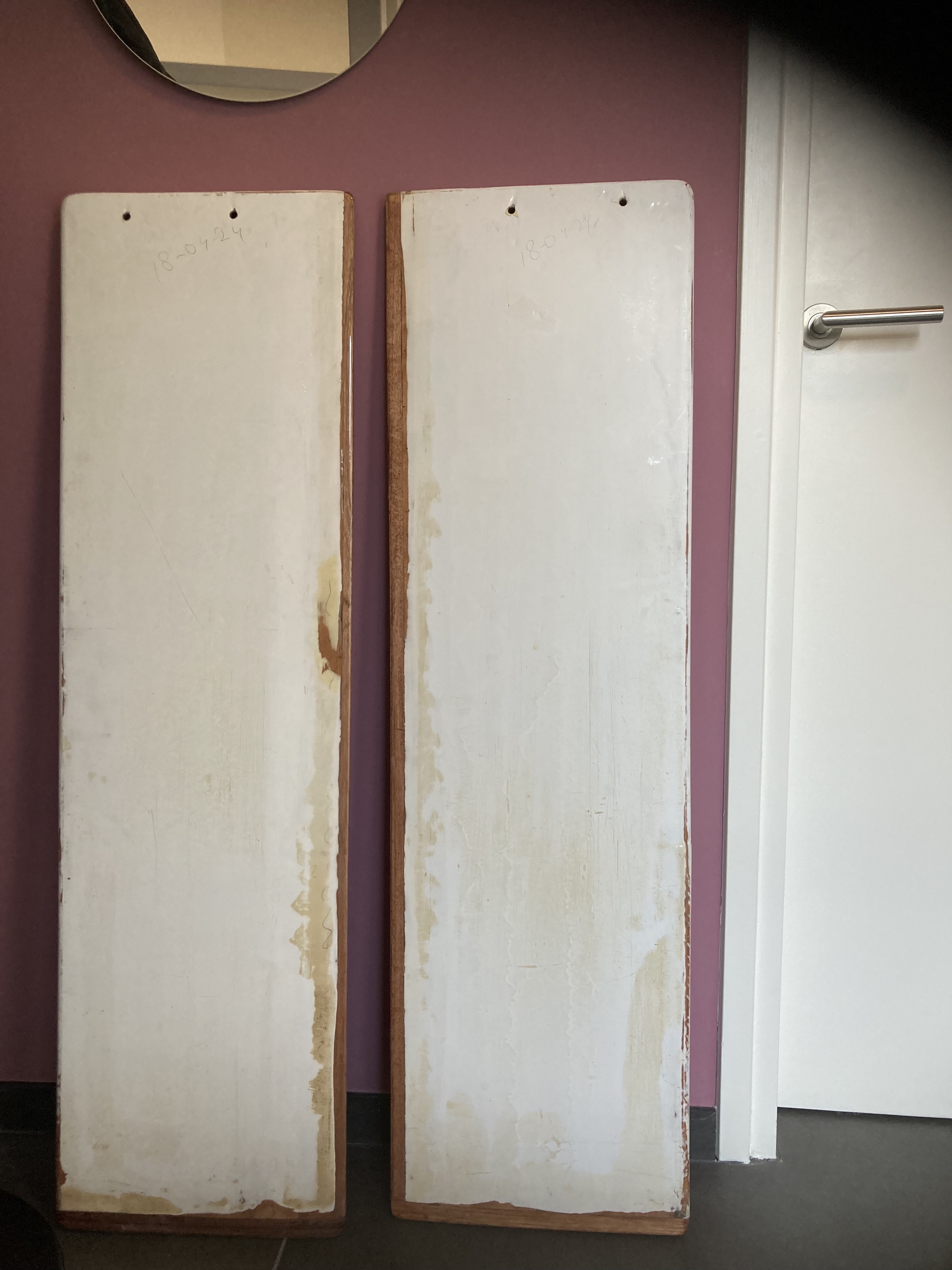
Existing foils with new trailing edges and hardwood shoes
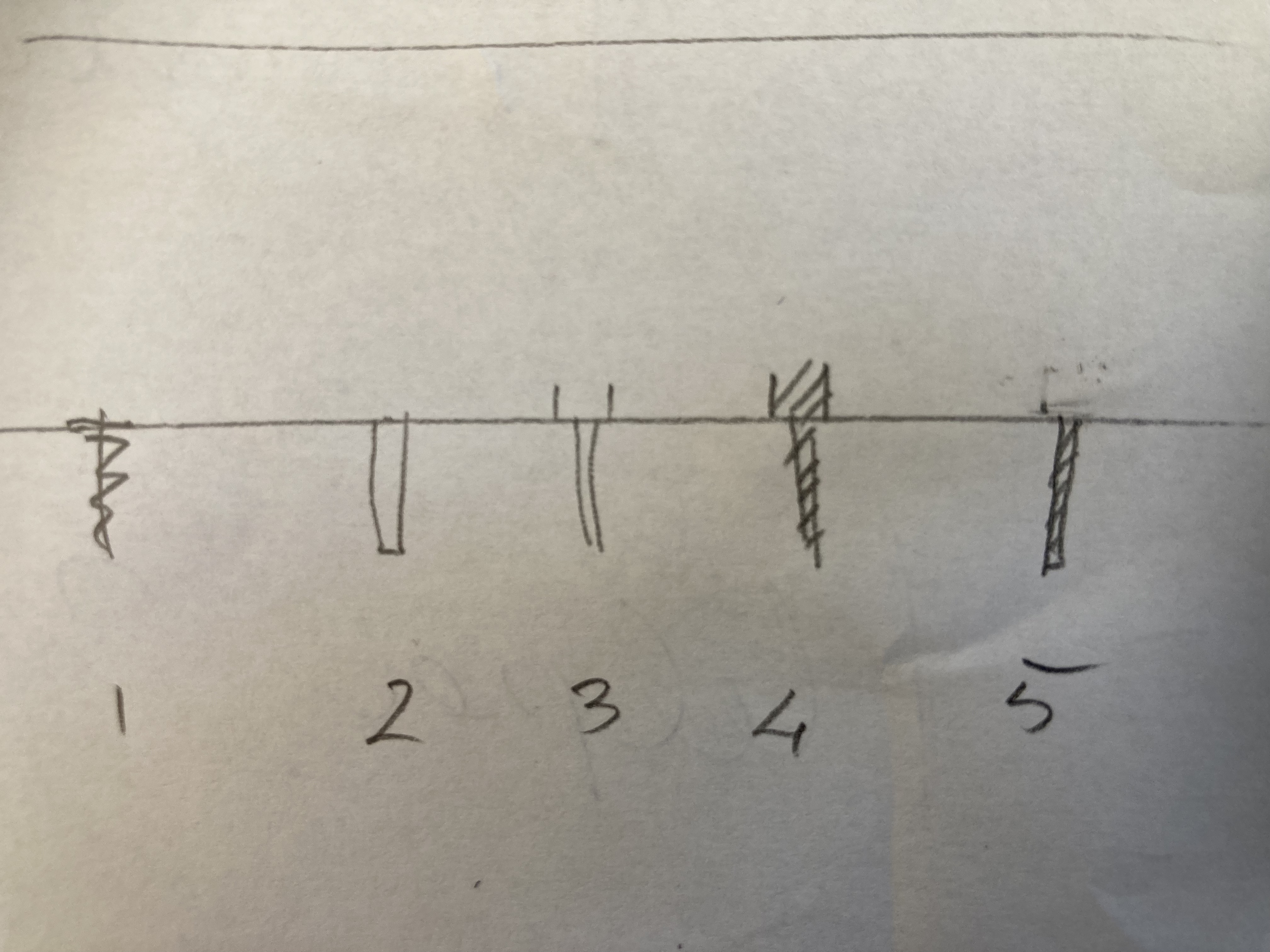
Filling screw holes in five steps.
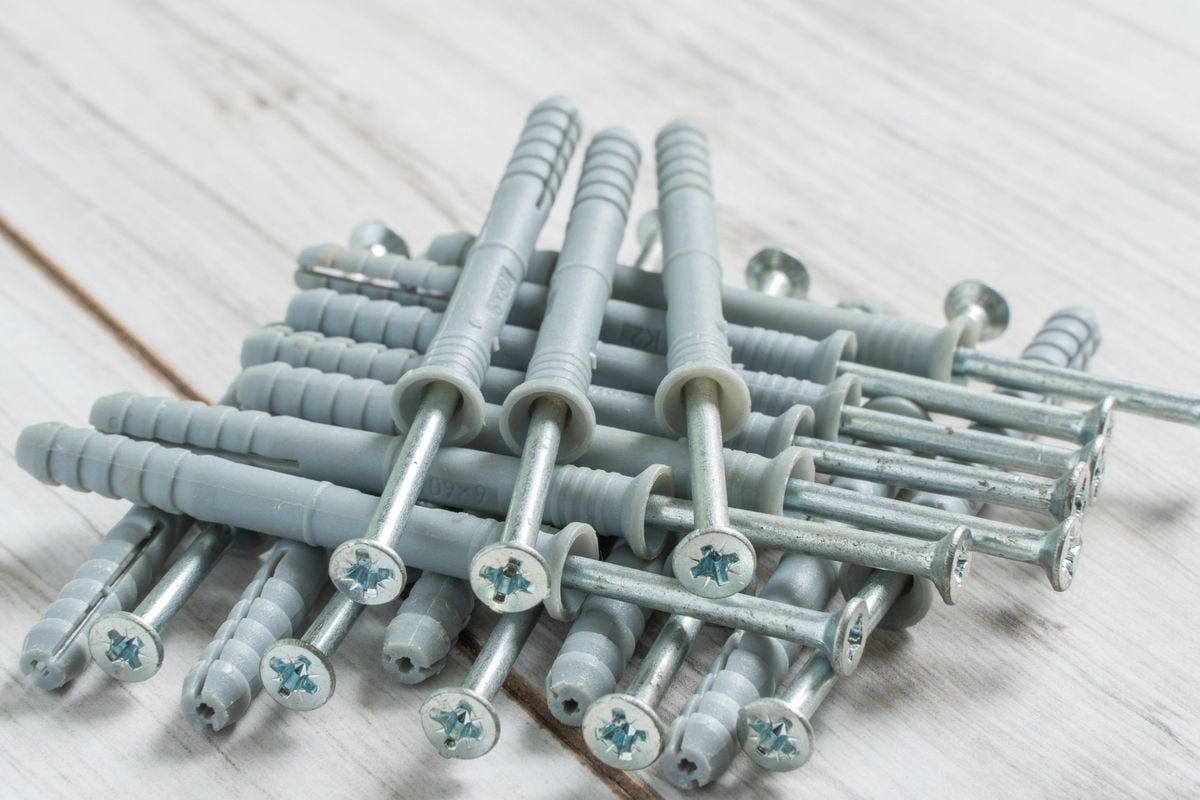
Wall plugs with epoxy around the screw holes.
|